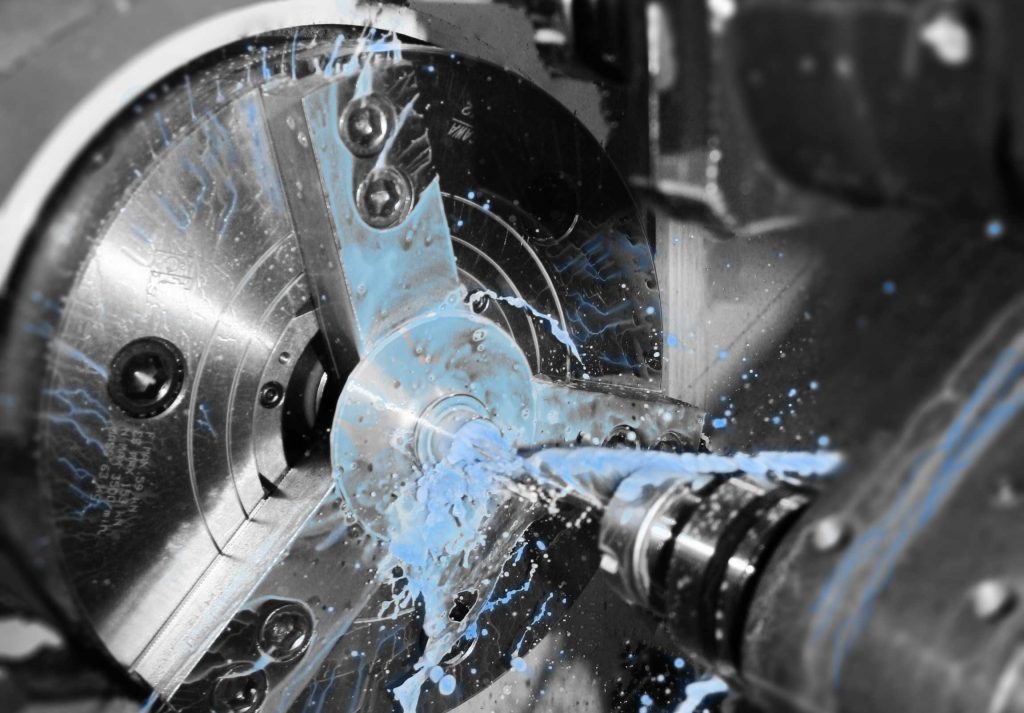
Five Steps to Improved Manufacturing Quality
By Jason Piatt, Industry Week
Good managers seek to contain costs in the manufacturing environment. There is no better cost to eliminate than the cost of poor quality. Scrap material and lost labor hours add no value to the operation.
In order to best eliminate these wastes, a strategic approach to quality improvement is essential. By following these five steps, quality can be improved in a meaningful, sustainable way.
1. Use a Team Mindset
Quality won’t be sustainably improved by individuals. To really make lasting and meaningful change in manufacturing processes, it will take a team-based approach. By involving multiple disciplines in the search for improved quality, a variety of perspectives is obtained. Also of importance is knowledge of process history. Why is the process the way it is today? There must be a reason or cause, and that reason should be considered so as not to repeat a problem of days gone by. By considering history and group perspective, solid improvements can be obtained.
2. Define Quality from the Customer Perspective
Too often, staff within a manufacturing environment want to make a product “better” but don’t really know what better means. With additional cost, we almost always can make a product better. But is additional cost desirable by the customer even if it means better product life? Someone in the organization should serve as the customer advocate. Typically this voice can come from the sales or marketing departments. Use the customers’ perspective to define what the best-in-class product would be and meet those requirements while minimizing cost.
3. Develop Organizational Understanding of the Cost of Quality
The cost to fix a defect in the field once it reaches a customer is dramatically higher than the cost to fix the source of the problem before it is created. It is essential that the manufacturing staff be trained to understand the cost multipliers involved with warranty repair or replacement and cost of damaged reputation. Once the staff take this perspective, a desire to find root cause for problem solving is inherently developed.
4. Solve Problems Completely
All too often, manufacturing quality improvements fix the symptoms of failure rather than the root cause. This can be done by adding quality inspection steps or rework stations that make it more efficient to fix defects. Instead, a true understanding of root cause should be developed within the teams. When teams develop the ability (through Ishikawa, fault tree, or five-why analysis) to ascertain root cause of defects in the manufacturing process along with a “killer test” that verifies the ability to turn-on and turn-off the problem in the manufacturing process, true solutions to problems will be created that will not allow the return of the issue.
5. Employ Strong Process Discipline
Throughout the quality improvement process, it is essential that strong process discipline is employed. Depending on the product that is being manufactured, deviation without proper team cooperation and anticipation of the change could have dire quality repercussions. While the organization should avoid cumbersome bureaucracy that inhibits innovation, it is essential that some structure be employed to maintain consistency and an understanding of the way the product is produced during that time period so that root cause can also be identified later if new problems arise as a consequence of the change.
By following these five steps, good management teams can develop great quality programs within their organizations.
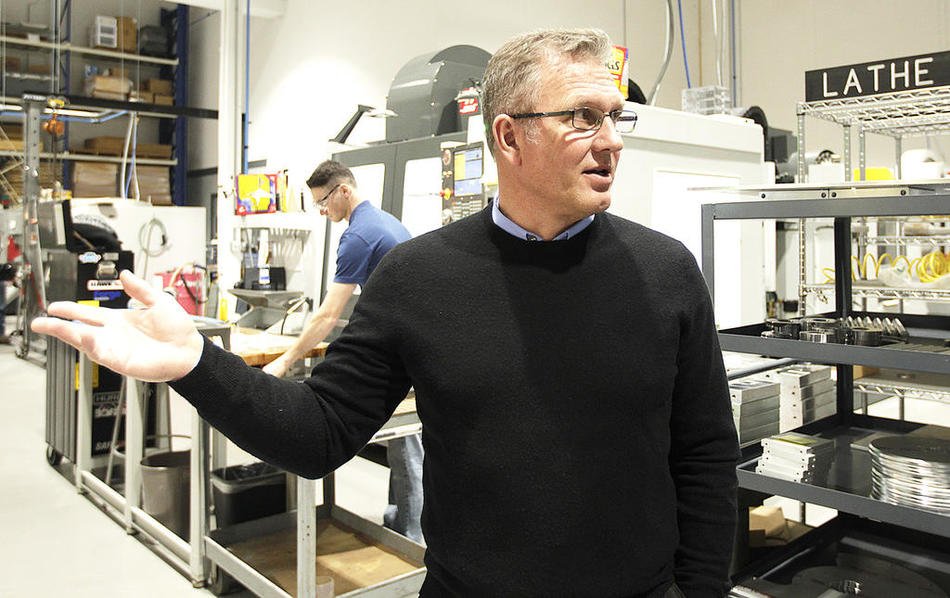
Manufacturer Vo-Tech doubles its space with Crystal Lake move
By STEPHEN Di BENEDETTO, Northwest Herald
The strategies that helped Vo-Tech, a midsized manufacturer in Crystal Lake, grow revenue during the past five years won’t change even though the company recently more than doubled its space.
A slow and steady approach has been the business mantra for Vo-Tech owner Wojciech Furman since the start of the decade.
Making machines and tools for companies in various industries, Vo-Tech prefers to add a few new customers, invest in the equipment and manpower to handle the new projects, and then repeat the plan.
The company now can show something for the strategy.
Vo-Tech earlier this year moved to a 35,000-square-foot building along Mitchell Court in Crystal Lake that it bought for $2.2 million.
Before the move, employees were feeling cramped in the company’s old 14,000-square-foot building along Tek Drive in the city, Furman said.
“We’ve been building revenue and customers. Sometimes, it just takes a long time before everything can mature,” he said. “We’ve been working on increasing production for the last five years. Finally now, this is the year where everything came together.”
With more room, Vo-Tech already has expanded production to keep pace with reinvestments being made by its largest customer base – nuclear power plants.
The new building also is large enough that Vo-Tech can slowly and steadily add employees and expand capabilities years from now, Furman said.
The business employs 22 people, a 57 percent increase from the 14 people employed when operations manager Mark Harper started at Vo-Tech four years ago.
Nuclear power plants have contributed greatly to the company’s increased workload, as the industry reinvests in aging plants with new equipment being made by Vo-Tech.
“Their machine shops were outfitted 30, 40 years ago with all that equipment,” Harper said. “It’s aging and getting to the point where they were ready to revamp.”
Vo-Tech initially relied on nuclear power plants when the business started in 1997.
Furman, who emigrated from Poland to Chicago in the 1980s and later moved his family to Lake in the Hills, started the business after years of traveling around the U.S. doing service work for the industry.
To diversify the business, Furman eventually extended his machine and tool production to manufacturing companies in other industries.
Vo-Tech also provides engineering services to all its customers, including ones in health care, food and agriculture.
It provides custom machines and tools for numerous companies in McHenry County.
“I don’t think we ever thought we end up with this beautiful facility. My idea for this business was to be able to always do the right thing. Take care of our customers, take care of employees, serve the community – do whatever you can do, but do it right,” Furman said. “I think it’s paying off.”